Introductory Musings on Industrial Warehouse Racking System
- Lauren Bracy
- Dec 15, 2023
- 4 min read
Updated: Mar 19
As a diligent observer of interior design and architecture trends, have you ever wondered what keeps the behind-the-scenes mechanism so sleek, especially in massive industrial warehouses? Where does the stock go? How is it managed? One might soon realise, much like the silent hero in an action movie, the unsung backbone to warehouse organisation lies in the aptly named warehouse racking system. This comprehensive blog post aims to delve deep into the intriguing world of various industrial warehouse racking types - an exploration of a vital but often overlooked aspect of Industrial Architecture.
The need here is to understand the array of storage options available in the industry, bringing together all the cons and pros, the applications and implications, unfolding design solutions on a grand scale. The mission is to provide a practical insight that goes well beyond the aesthetic aspects of design and décor. A granule understanding of warehouse racking types could prove essential to efficient warehouse management and invaluable for designers involved in industrial architecture.
Are you ready to follow along on this exploration journey? Are you inquisitive about the stalwart heroes contributing to the massive industry where orderliness is an immediate necessity and not mere ornamentation? If so, let’s dive into our chosen topic — an exploration of industrial warehouse racking—and get lost in its myriad of details, the sheer utility and the understated aesthetic of industry practicality.
The Essence of Warehouse Racking: Why is it Crucial?

The name in itself is reflective of the function, but why is the warehouse racking system such a mandatory requirement? Stringent time constraints, an unforgiving pace, challenging space issues, and above all, safety—these are the confluence of factors that necessitates a well-organised system. By optimising space, warehouse racking systems ensure maximum usage of available area, promoting efficiency, and productivity.
The system also lays the foundation to accommodate a variety of products in a safe and orderly manner, reducing the chance of stocking errors or misplaced items. The introduction of a warehouse racking system promotes the safe handling of goods and minimises potential injury risks associated with manual handling.
Does it raise the question of which racking system to introduce in your industrial warehouse? That’s precisely where we are headed. After all, making the right choice among the different types of industrial warehouse racking is half the battle won.
Selective Racking: An Overview of the Most Common Type
Stepping first into the realm of warehouse racking types, we encounter selective racking. As the most commonly applied system, the model’s selling points include both cost-effectiveness and direct access to all pallets.
Pallets in a selective racking system are located on continuous rails that permit movement in a forward and backward fashion. It leaves the aisle space available to forklifts for immediate access to stored goods. Before opting for this system, however, it would be wise to consider the warehouse space available since it requires numerous aisles.
While selective racking holds popularity due to its easy accessibility and cost advantage, it might not be the optimum choice for warehouses with limited space or those housing a variety of products with less quantity of each. This brings us to more specialised warehouse racking systems—dive in, shall we?
Pallet Flow Racking: The High-Density Storage Solution
Welcome to a system that provides high-density storage without compromising accessibility. Enter pallet flow racking, innovatively designed with inclined rails and rollers with pallet loads following the first-in-first-out (FIFO) retrieval system.
Highly efficient for time and space, the pallet flow racking system works brilliantly for warehouses dealing with perishable items requiring quick turnover. The main advantage is the automatic stock rotation following FIFO, which ensures no products stay beyond their expiry.
However, before running to implement this system, one must weigh the high cost associated with the initial set up of the pallet flow racking system. It is not a budget-friendly option and is only justifiable for businesses with high rotation products and large volumes.
Cantilever Racking: The Response to Bulky Loads
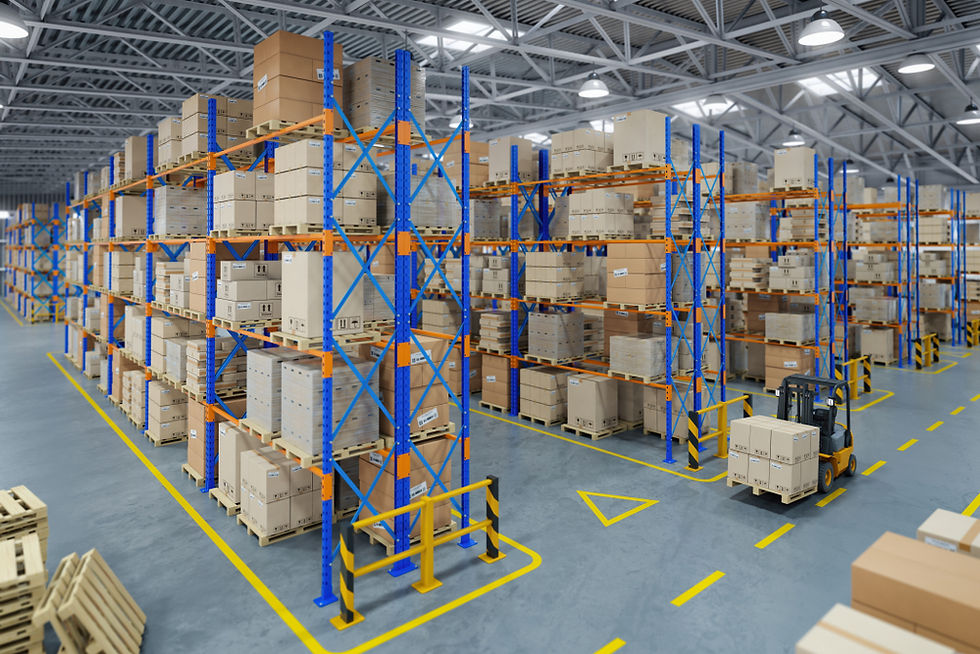
For warehouses storing long and bulky items like timber, piping, or panels, cantilever racking comes to the rescue. The structure comprises a vertical column, arms extending horizontally, and a stable base, thus ensuring excellent support for bulky loads.
The openness at the front allows for easy placement and retrieval of goods, with access possible by forklifts or manually. It’s versatile, expandable, and offers a high holding capacity but is not the best fit for warehouses stocking palletised goods or items of varying lengths.
Drive-In/Drive-Thru Racking: The Ultimate Space Saving Option
For the space-conscious warehouse managers, drive-in/drive-thru racking offers an appealing choice. By reducing aisles and lanes, these systems provide an excellent space-saving option, operating on either the first-in-last-out (FILO) or FIFO system.
Though they offer significantly increased storage capacity, the possibilities of the pallet or the racking system's damage are inevitable due to close interaction with forklifts. They are, hence, more suitable for sturdy goods and those with low rotation.
Concluding Thoughts on Industrial Warehouse Racking
Industrial warehouse racking a testament to organized chaos, with each type espousing a unique appeal based on individual warehouse needs. Choices abound from the common but effective selective racking to the high-density storage offered by pallet flow racking, each holding merits and constraints concerning cost, space, and type of goods stored. The key lies in understanding these nuances and making an informed decision that serves the warehouse's flow, space, and economic demands.
These racking heroes often escape recognition but constitute an integral aspect of a functioning warehouse system. In the grand schema of Industrial Design, every bolt, every beam, every pallet matters. As we continue exploring further aspects of design and architecture systems, let's take a moment and celebrate these unsung, effective, and fundamental features of any industrial setup. Remember, a well-organised warehouse is a well-functioning warehouse.
Comentários