The Advantages and Challenges Associated with Pneumatic Conveying
- idavisnancy
- Sep 28, 2019
- 3 min read
A pneumatic conveying system works on air or gas to transport bulk materials from their source to destination. The material to be transferred is subjected to the force of pressure by the gas or air through an enclosed pipeline. The airflow that is used to move the materials through the pipeline is provided by air movers like vacuums or positive displacement blowers. Hence, by making the best use of airflow and pressure difference, the system transports materials over particular distances with sufficient ease
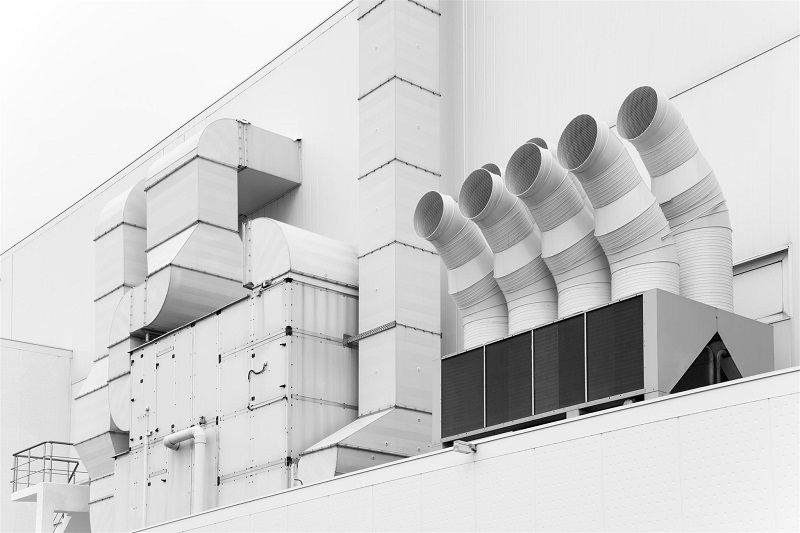
Pneumatic conveying systems are known to be cheap and reasonable than other systems, as they are fully enclosed, can be controlled to a certain extent, and are modifiable. They are also an environmentally cleaner option due to their enclosed characteristic so that conveying materials can be kept clean and free of any foreign matter. There are many advantages as well as challenges with this type of conveying system and we shall take a look at them in the following sections.
Advantages of pneumatic conveying
Unlike other industrial conveying systems, pneumatic conveying provides a lot of advantages, some of which are detailed over here.
There is enough flexibility – This type of conveying system can be easily routed as per the requirements of the user. They can also be designed near existing equipment, can be run vertically or horizontally, can run over obstructions or any type of convoluted path, and can go over long distances. Therefore, it offers ample flexibility for users and that is a major advantage.
Very easy to install – Pneumatic conveying systems are comparatively lightweight than other conveying mechanisms, which is why they don’t require heavy structural support for installation and operation. It can reduce a lot of construction-related issues that can be time-saving for any industry. You can also save sufficient space by installing this type of conveying system.
Maintenance is not a problem – A pneumatic conveying system primarily consists of a pump, tubing, separator and an in-feed system. In case of a breakdown, each of them can be repaired independently without disturbing the other parts. Thus, maintenance can be completed fast and the machine outage can be minimized.
Spectacularly adaptable – Pneumatic systems adapt conveniently to existing machines, which means that beginning from the start is not required for its installation. Moreover, a large number of discharges and pick-up points can be made for the system. Therefore, it is quite adaptable to any industrial environment.
Challenges associated with pneumatic systems
There can be some typical challenges while using a pneumatic conveying machine, and some of them are highlighted here for proper understanding.
Miscalculating pressure drop – There are many parameters in the system like line layout, particle and pipe size, product density, etc. Over a line, finding out the pressure drop correctly can be one of the biggest challenges of the system. A problem in it can have a recurring issue with the other parameters, but luckily there is software available for it that can help to correctly determine the needed pressure drop. Therefore, investing in software can be a very plausible decision.
Incorrect flow rate – It is a type of common designing error, as the average flow can be a disadvantage because a consequence of it can be blow line plugging. Production rates can always differ between companies, and it is usually desired that a particular system should work at its peak flow. Therefore, while designing a system, this point must be kept in mind.

These are some of the challenges that can be expected from the system and careful analysis can help in avoiding them. By using pneumatic conveying, a working and efficient system can be realized that can help in the production process.
Comments